PROCESSING FACILITY
The Bucko Lake operation is designed to treat 1,000 dry tons per day of nickel-bearing ore from the underground mine on the basis of a 24 hours a day, 7 days per week operation. The ore from all mining activities is processed at this facility to produce a nickel sulfide concentrate that is shipped under the terms of an offtake agreement with Glencore to smelting facilities in Sudbury, Ontario.
Additional information on the milling operations appears below:
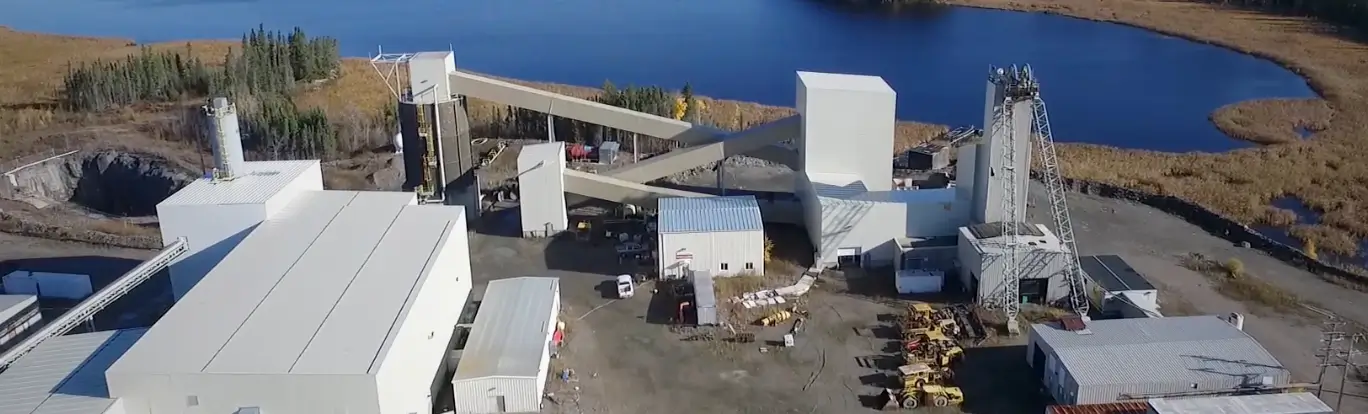
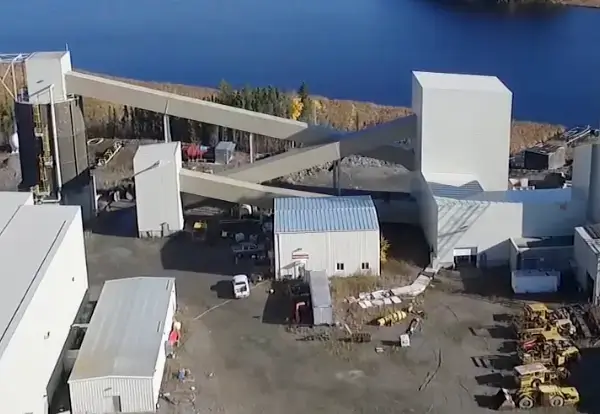
Crushing and Storage Area
Ore from the underground mine is trucked via a spiral haulage way to surface and stored in the coarse ore shaft bin. The underground run of mine ore is sized through a jaw crusher and cone crusher, series of transfer conveyor belts and vibratory triple deck screen. The jaw crusher sizes the material to 3” (76 mm). The 3-foot (0.9 m) cone crusher then sizes the mill feed product to 5/8 inch (1.6 cm) or less and is directed to a fine ore bin. Four vibrating feeders located under the fine ore bin are used to feed the crushed ore at a controlled rate to the rod mill which is situated in the main mill building.
The grinding circuit comprises a rod mill equipped with a 450-horsepower motor followed by a ball mill equipped with a 1,500-horsepower motor. The discharge product from both mills is pumped from the cyclone feed pump box to a cyclone cluster from which the overflow sizing 80% passing 98 microns is routed to the flotation circuit. The underflow from the cyclone cluster, comprising two 457 mm diameter cyclones, is recycled to the ball mill.
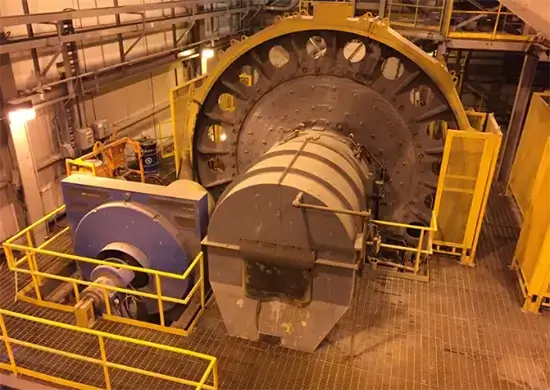
FLOTATION
The flotation circuit is comprised of a rougher/scavenger stage (five cells) and three cleaner stages. The cleaner circuits consist of five primary cells, three secondary cells, and two tertiary cells. The rougher circuit is fed from the second of two conditioners, which are used to mix the initial dose of reagents with the grinding circuit product. The tailings product from the scavenger cells is combined with the primary cleaner tailings and pumped to either the tailings dam or the backfill plant. The tertiary cleaner concentrate is the final product and is pumped to the concentrate thickener and filter section for dewatering.
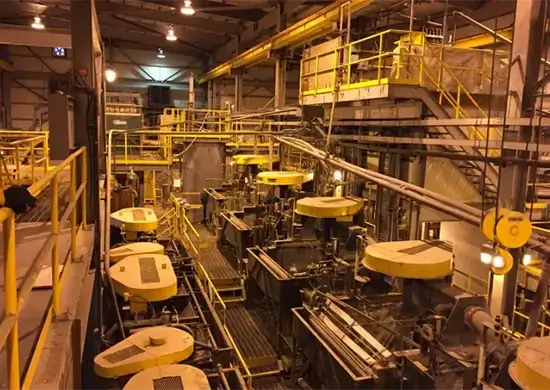
Concentrate Dewatering
The overflow from the 5-m-diameter thickener discharges into the process water tank while the underflow is pumped to the 5.1-m-diameter concentrate stock tank. The concentrate stock tank is sized to hold 18 hours of flotation concentrate. The thickener operates continuously while the filter circuit operates 12 hours per day. The thickened concentrate is pumped at a controlled rate from the stock tank and fed to a Larox Filter. The filtrate product from the Larox Filter is recovered containing approximately 8% moisture, is emptied into a concentrate load-out storage area. The concentrate is periodically loaded into trucks and transported to concentrate handling facilities in Winnipeg before it is transferred to rail for shipment to smelting facilities owned by Glencore in Sudbury.

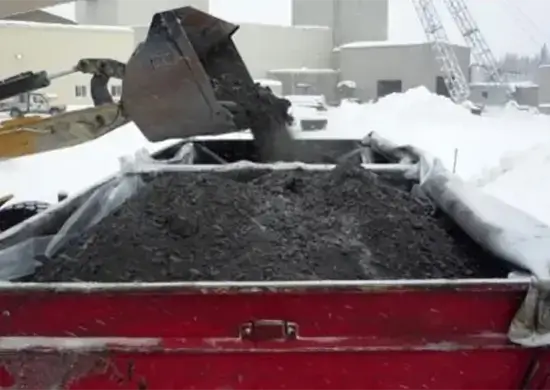
BACKFILL PLANT
A backfill plant was designed in 2012 to supply the underground mine with paste backfill. All surface construction and equipment were completed and the plant received engineering and electrical certification. However, due to the suspension of operations at Bucko Lake Mine, commissioning of the paste backfill plant was placed on hold in 2012. To date, a total of C$5.9 million in expenditures were incurred in the construction of the paste backfill plant
Design: A dedicated pump attached to the final tailing pump box delivers tailings to the backfill cyclone cluster. The backfill cyclone cluster comprises three operating and one standby hydro cyclone. The cyclone overflow, containing approximately 15% solids by weight, gravitates to the flotation tailings pump box while the underflow goes directly into a slurry tank and is pumped into the twin screw and mixed with sand and cement. The undersize from the screen is pumped back to the flotation tailings pump box and the oversize is conveyed to a stockpile. This stockpiled material is reclaimed using a front-end loader and mixed with water and cement in the backfill slurry batch mixing tank. When required underground, the paste backfill is pumped from the batch mixing tank through a borehole to the underground distribution system.
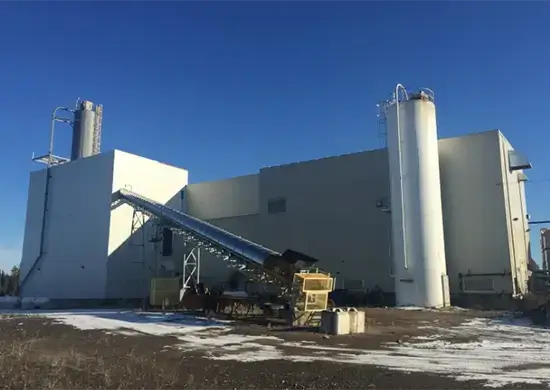
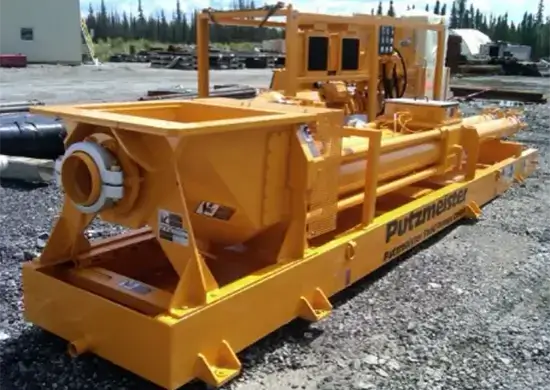
Tailings Management Area
The TMA has a footprint of approximately 65.5 hectares to store all tailings from Bucko Lake Mine for the remainder of its existing mine life. Environmental studies indicate that the TMA would have a net benefit in relation to the environmental impact, eliminating the need for subaqueous deposition of the tailing into Bucko Lake. The construction of the TMA was carried out in two phases and Phase I construction was completed and put in use in March 2012 for total expenditures of $5.5 Million.
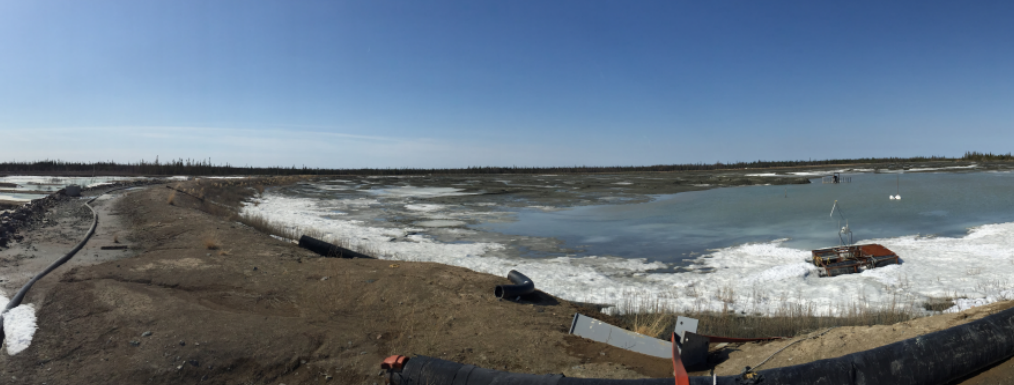
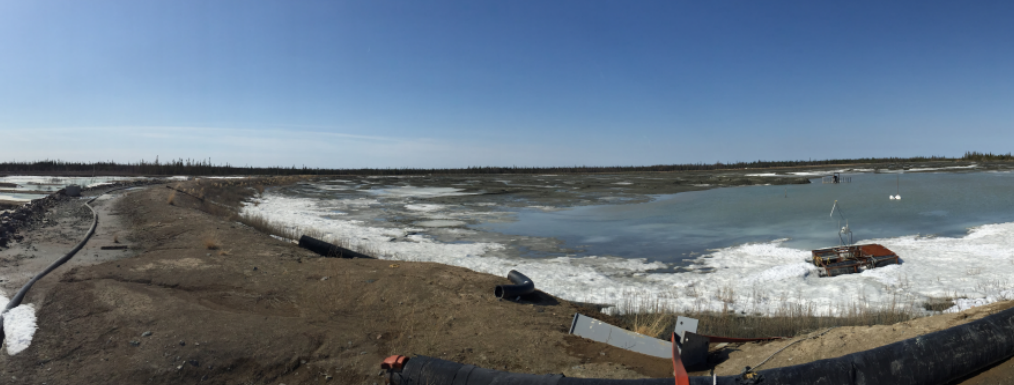
Plant Utilities, Services and Water Systems
A low-pressure air blower, plant air compressor and instrument air compressor with ancillaries are included within the scope of concentrator building services. The reclaim water pumps and line from the tailings deposition area feed the process water tank which is situated near the main process building. Process water pumps are utilized to feed the process water distribution system. Emergency water demand is also supplied from the process water tank. Fresh water in the plant is used for the potable water system, gland seal water and the fresh water distribution system.